Palazzo Europa: l’ingegneria digitale per la sede del Consiglio Europeo e dell’UE
L'ingegneria digitale migliora l'efficienza della progettazione e della produzione edile attraverso l'ottimizzazione dei processi e la riduzione dei tempi.
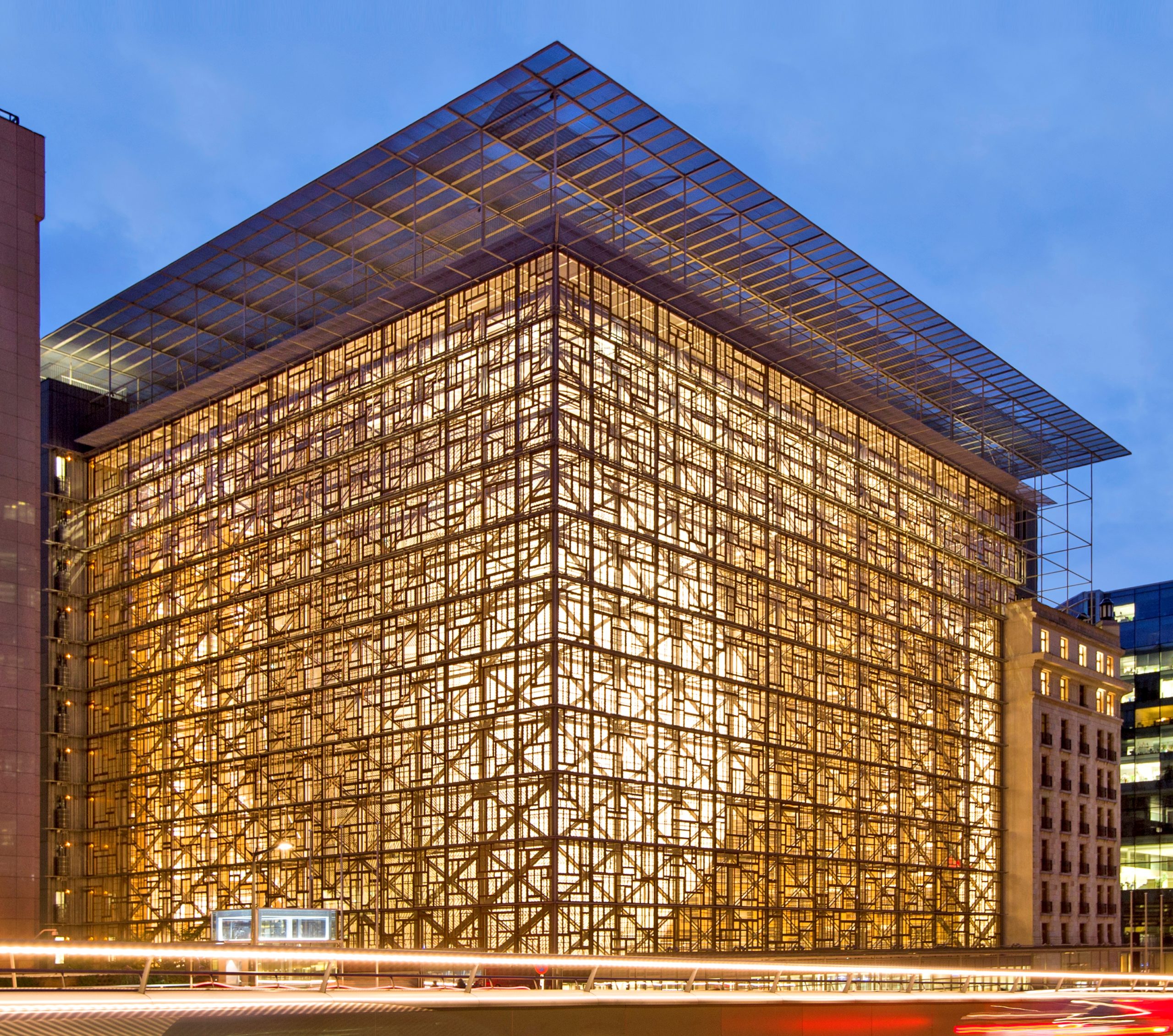
L’ingegneria digitale consente di migliorare l’efficienza della progettazione e della produzione edile, attraverso l’ottimizzazione dei processi e la riduzione dei tempi. Grazie all’utilizzo di un ambiente informativo unificato, i progettisti possono simulare, sperimentare e validare ogni componente, permettendo di perfezionare e velocizzare le attività in cantiere. L’Ingegneria digitale rappresenta la tecnologia all’avanguardia che consente di creare un modello digitale tridimensionale, basato su parametri elaborati da algoritmi pre-programmati.
La modellazione parametrica, infatti, è stata la chiave del successo per la realizzazione della fascia esterna della lanterna del Palazzo Europa, la sede principale del Consiglio europeo e del Consiglio dell’Unione Europea a Bruxelles. Il progetto, originariamente concepito come un intervento di ristrutturazione e ampliamento di un edificio storico, è stato sviluppato dal team di architetti composto da Studio Valle, Philippe Samyn and Partners e Buro Happold. La particolarità dell’opera consiste nell’essere composta da un volume esterno cubico che racchiude un volume interno, la cosiddetta “lanterna”.
Quest’ultima è caratterizzata da una struttura multilivello con sezione ellittica variabile, che ospita sale riunioni, conferenze e spazi per la stampa. Grazie alla modellazione parametrica, l’intero processo di progettazione e produzione è stato finalizzato in pochi mesi, dimostrando l’efficacia dell’Ingegneria digitale nell’ottimizzazione dei processi edilizi. Andando maggiormente nei dettagli, il volume ellittico della lanterna è stato generato dalla sovrapposizione di diverse ellissi, che si allargano al centro per posizionare gli spazi di minori dimensioni nei livelli superiori e inferiori, mentre la sala più grande con 250 posti si trova nella sezione centrale più ampia. Durante la notte, la struttura è illuminata da 374 tubi a LED, integrati all’interno dell’involucro esterno, che proiettano la luce sulla trama obliqua dei pannelli di vetro curvi che lo rivestono, dando vita ad una grande e suggestiva lanterna luminosa lungo Rue de la Loi.
Lo studio italiano VLP+P ha risolto la complessità realizzativa della pelle della lanterna, ottimizzando l’intero processo di studio e definizione dei requisiti configurativi, grazie all’impiego di tecniche di ingegneria digitale. Utilizzando la piattaforma 3DEXPERIENCE di Dassault Systèmes, i progettisti hanno creato un modello digitale dell’opera, che ha consentito di studiare in un ambiente virtuale geometrie, angoli di curvatura e tolleranze, con una capacità elaborativa potenziata che ha perfezionato i risultati e accelerato i tempi e le modalità di sviluppo e produzione.
Per approfondire il progetto della lanterna del Palazzo Europa, è interessante notare come la struttura si estenda su 12 piani e sia rivestita in vetro a doppia curvatura. Il team di VLP+Partner si è trovato di fronte a diverse sfide durante il processo di realizzazione. La prima sfida riguardava l’attuabilità dell’idea architettonica rispetto alle tecniche produttive disponibili, mentre la seconda sfida era legata alla progettazione di tutti i sistemi di staffeggio in acciaio, caratterizzati da diverse configurazioni geometriche. La terza sfida importante, infine, era quella di progettare la compartimentazione al fuoco nel modo migliore possibile. Per quanto riguarda la doppia curvatura delle lastre in vetro, la tecnologia consentiva di fare curvature con raggi differenti su ciascun pezzo, ma ciò avrebbe comportato tempi di realizzazione troppo lunghi.
Utilizzando l’ingegneria digitale, le lastre vetrate sono state ottimizzate per essere prodotte in singola curvatura. Il team di VLP+P ha utilizzato la modellazione parametrica per generare un gemello virtuale della lanterna, partendo dallo studio della superficie di una prima lastra con una curvatura variabile da 15 m a 17 m. Sostituendo il vetro a doppia curvatura con elementi cilindrici più facili e meno costosi da produrre, gli esperti hanno identificato l’asse del cilindro che approssimava al meglio la superficie reale della lastra. Questo cilindro ha permesso di effettuare le opportune verifiche tra la superficie iniziale e quella ottimizzata, confermando tolleranze e differenze talmente minime da garantirne la riproducibilità in cantiere.
Grazie all’ingegneria digitale, VLP+Partner ha affrontato questa sfida in modo brillante. Ogni vetro della pelle della lanterna è dotato di un nodo con una staffa in acciaio che può assorbire delle tolleranze, ad esempio allungarsi o ruotare per assumere diverse configurazioni geometriche. L’azienda ha modellato virtualmente tutte le staffe in tutte le 1700 relative posizioni e, sulla base del rilievo ottenuto tramite tecnica laser scanner, ha provveduto a contestualizzare virtualmente il sistema di staffeggio nella posizione reale. In questo modo, è stato possibile regolare ogni staffa nella configurazione corretta che doveva assumere in cantiere, fornendo al produttore dati precisi relativamente all’estensione, nonché ai corretti angoli in pianta e in prospetto delle staffe. Grazie all’ingegneria digitale, il processo di montaggio in cantiere è stato accelerato, risolvendo in modo efficiente una delle sfide più complesse del progetto.
Per garantire la resistenza al fuoco e la compartimentazione dei piani, sono state utilizzate lastre di vetro ignifughe in fermacell, le quali necessitavano di una struttura d’acciaio per sostenerle. Questa struttura doveva essere flessibile e adattarsi a diverse pendenze e angoli dell’edificio. Grazie alla loro adozione di un ambiente comune di dati, il flusso di informazioni tra i team è diventato più fluido che mai, dalla fase di concept architettonico alla costruzione sul campo. L’ingegneria digitale ha reso possibile una cooperazione senza precedenti, consentendo una maggiore efficienza e tempi di realizzazione più rapidi.