Cellulosa: un nuovo materiale per la stampa 3D
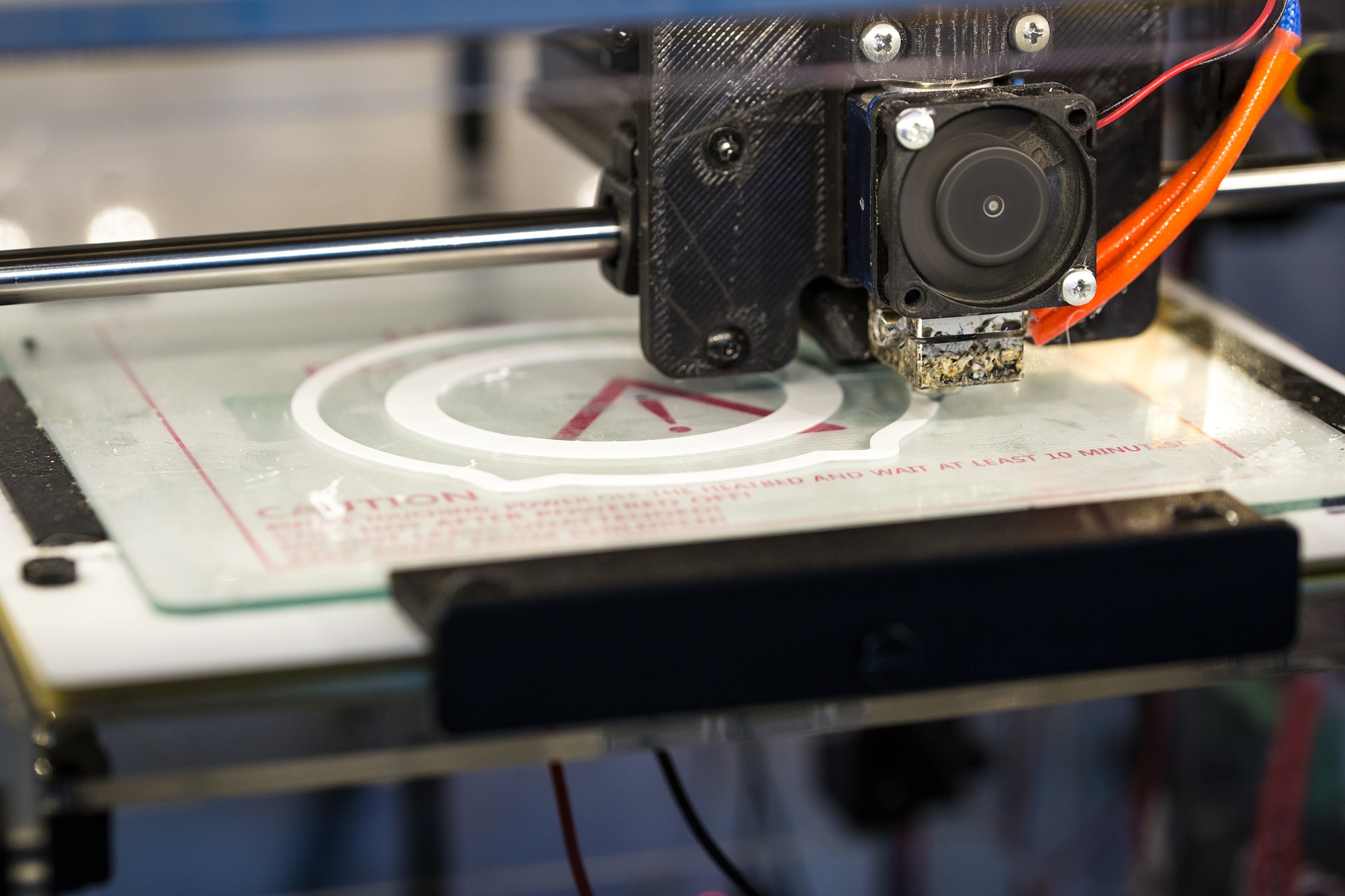
Le piante lo fanno da sempre: producono la cellulosa e la usano per costruire strutture complesse con straordinarie proprietà meccaniche.
Le sue caratteristiche naturali rendono la cellulosa attraente per gli scienziati dei materiali che stanno cercando di produrre prodotti sostenibili con funzioni speciali. Tuttavia, la trasformazione di materiali in strutture complesse ad alto contenuto di cellulosa è ancora una grande sfida per gli scienziati dei materiali.
Un gruppo di ricercatori dell’ETH di Zurigo ed Empa ha ora trovato il modo di elaborare la cellulosa usando la stampa 3D in modo da creare oggetti di complessità quasi illimitata che contengono alti livelli di particelle di cellulosa.
Per fare questo, i ricercatori hanno combinato la stampa tramite il metodo DIW (Direct Ink Writing) con un successivo processo di densificazione per aumentare il contenuto di cellulosa dell’oggetto stampato ad una frazione di volume del 27%.
Il loro lavoro è stato recentemente pubblicato sulla rivista Advanced Functional Materials.
I ricercatori ETH ed Empa non sono certo i primi a trattare la cellulosa con la stampante 3D. Tuttavia, i precedenti approcci, che utilizzavano anche inchiostro contenente cellulosa, non sono stati in grado di produrre oggetti solidi con un contenuto e una complessità di cellulosa così elevati.
La composizione dell’inchiostro con cellulosa da stampa è estremamente semplice. Consiste solo di acqua in cui sono state disperse particelle e fibre di cellulosa che misurano alcune centinaia di nanometri. Il contenuto di cellulosa è compreso tra il 6% e il 14% del volume di inchiostro.
I ricercatori dell’ETH hanno usato il seguente trucco per densificare i prodotti stampati di cellulosa: dopo aver stampato un inchiostro a base di cellulosa, hanno messo gli oggetti in un bagno contenente solventi organici.
Poiché la cellulosa non ama i solventi organici, le particelle tendono ad aggregarsi.
Questo processo si traduce in un restringimento della parte stampata e di conseguenza in un aumento significativo della quantità relativa di particelle di cellulosa all’interno del materiale.
In un ulteriore passaggio, gli scienziati hanno immerso gli oggetti in una soluzione contenente un precursore di plastica fotosensibile.
Rimuovendo il solvente per evaporazione, i precursori di plastica si infiltrano nell’impalcatura a base di cellulosa.
Successivamente, per convertire i precursori di plastica in una plastica solida, hanno esposto gli oggetti alla luce UV. Questo procedimento ha prodotto un materiale composito con un contenuto di cellulosa del 27% in volume.
Il processo di densificazione ci ha permesso di iniziare con un 6-14% in volume di miscela di acqua e cellulosa e di finire con un oggetto composito che mostra fino al 27% in volume di nanocristalli di cellulosa
afferma Hausmann.
Inoltre, a seconda del tipo di precursore di plastica utilizzato, i ricercatori possono regolare le proprietà meccaniche degli oggetti stampati, come la loro elasticità o resistenza. Ciò consente di creare parti rigide o morbide, a seconda dell’applicazione.
Usando questo metodo, i ricercatori sono stati in grado di fabbricare vari oggetti compositi, tra cui alcuni di natura delicata, come oggetti di uno spessore di solo 1 millimetro.
Tuttavia, la densificazione delle parti stampate con uno spessore delle pareti superiore a cinque millimetri porta alla distorsione della struttura perché la superficie dell’oggetto densificante si contrae più velocemente del suo nucleo.
I ricercatori hanno studiato i loro oggetti utilizzando analisi a raggi X e test meccanici.
I loro risultati hanno mostrato che i nanocristalli di cellulosa sono allineati in modo simile a quelli presenti nei materiali naturali.
Questo significa che possiamo controllare la microstruttura di cellulosa dei nostri oggetti stampati per produrre materiali la cui microstruttura ricorda quella dei sistemi biologici, come il legno
afferma Rafael Libanori, del gruppo di ricerca del professor ETH André Studart.
Le parti stampate sono ancora di piccole dimensioni, ma ci sono molte potenziali applicazioni, dall’imballaggio personalizzato agli impianti di sostituzione della cartilagine per le orecchie.
I ricercatori hanno anche stampato un orecchio basato su un modello umano.
Per utilizzare un prodotto creato con questa tecnica e utilizzarlo nella pratica medica, tuttavia, sono necessarie ulteriori ricerche e, soprattutto, studi clinici. Ne abbiamo parlato anche qui.
Questo tipo di tecnologia della cellulosa potrebbe anche interessare l’industria automobilistica. Le case automobilistiche giapponesi hanno già realizzato un prototipo di un’auto sportiva per la quale le parti della struttura sono realizzate quasi interamente con materiali a base di cellulosa.
Qui lo studio completo:
- Complex‐Shaped Cellulose Composites Made by Wet Densification of 3D Printed Scaffolds (onlinelibrary.wiley.com)
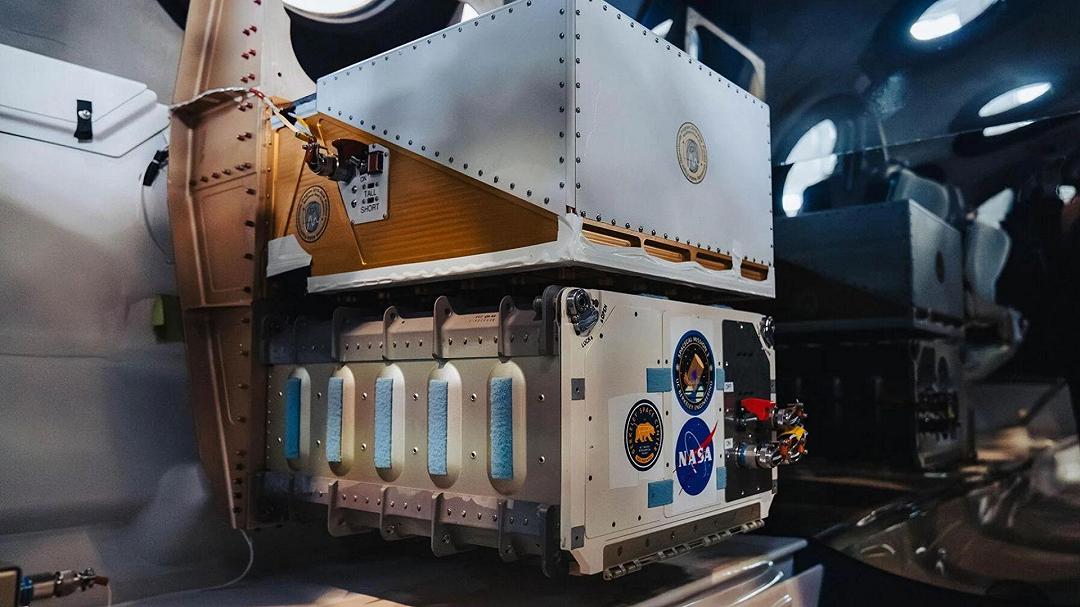
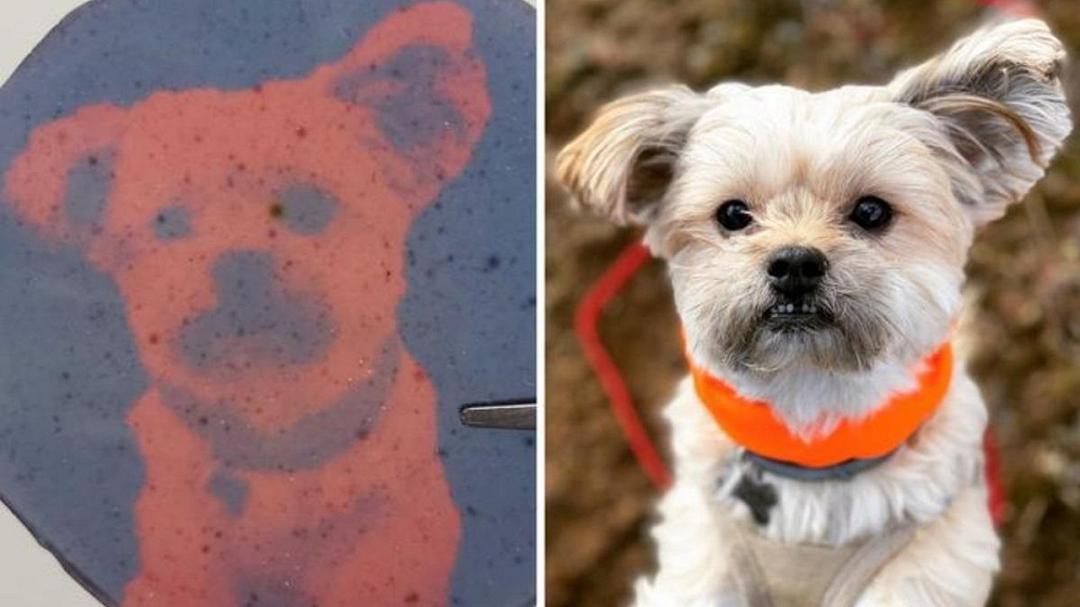
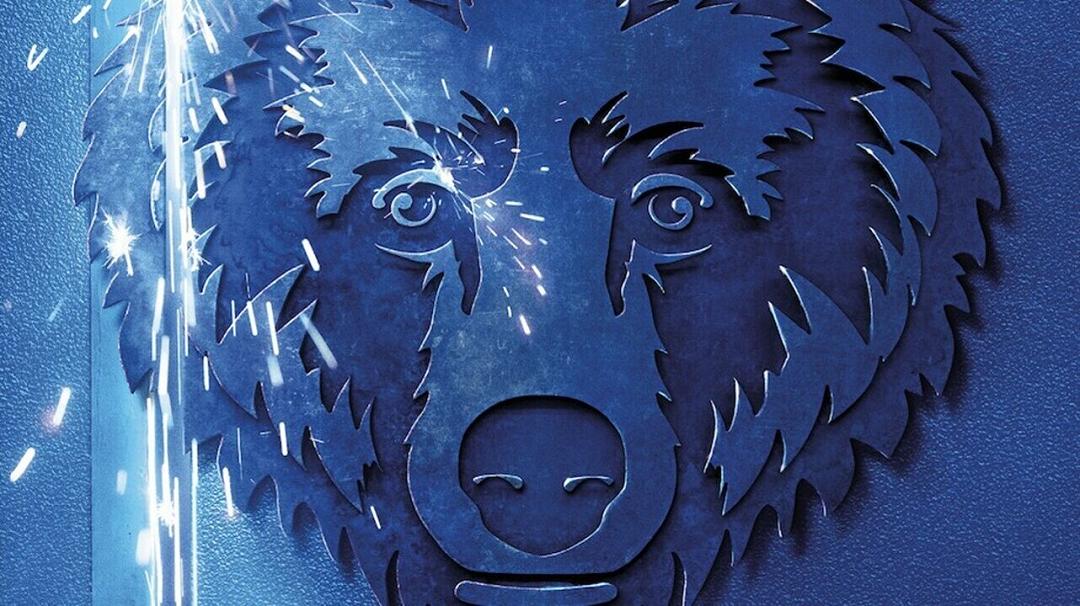