SR-71: la Costruzione
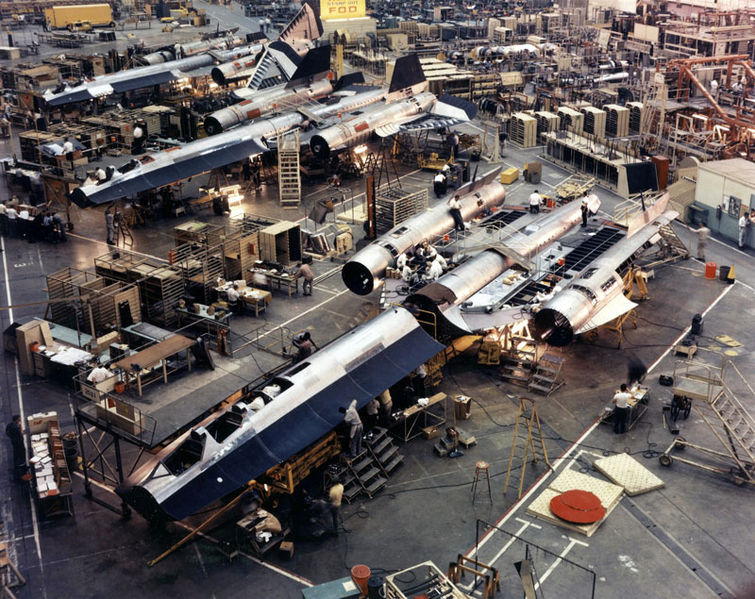
Nello scorso articolo abbiamo parlato di come sia nato, vissuto ed andato in pensione l’aereo più arrogante di sempre. Ma al di là della sua storia, cos’è che rende questo veicolo così speciale?
Essenzialmente il fatto che con le conoscenze tecnologiche di allora era praticamente impossibile realizzare un mezzo simile.
Ma come tutti sappiamo gli Skunk Works sono riusciti lo stesso nell’impresa.
Andiamo ora a vedere un po’ più da vicino alcuni dei problemi più grossi che si sono trovati ad affrontare ed i modi brillanti, e a volte incredibili, in cui li hanno risolti.
I materiali e la temperatura
Il primo e più grosso scoglio che incontrano i nostri super progettisti si presenta subito nei primi stadi dello sviluppo: uno dei requisiti fondamentali che devono tassativamente essere rispettati è quello della velocità superiore a Mach 3.
Nonostante gli sforzi fatti nelle fasi di design per ottenere una sagoma il più possibile aerodinamica, ci si è resi conto immediatamente che un qualsiasi mezzo operante a quelle velocità sarebbe andato incontro a massicci incrementi di temperatura, anche nell’atmosfera rarefatta ad alta quota.
Come si può facilmente capire due sono le cause principali del fenomeno del riscaldamento: l’attrito aerodinamico e la presenza dei propulsori.
I ragazzi degli Skunk Works procedono quindi a fare qualche stima preliminare sull’entità e l’importanza di questi due fenomeni, ed i risultati sono parecchio preoccupanti: le temperature attese lungo i profili più esterni si collocano in un range compreso fra i 230° ed i 380°, mentre nelle zone di telaio più vicine ai reattori si raggiungono addirittura i 600°.
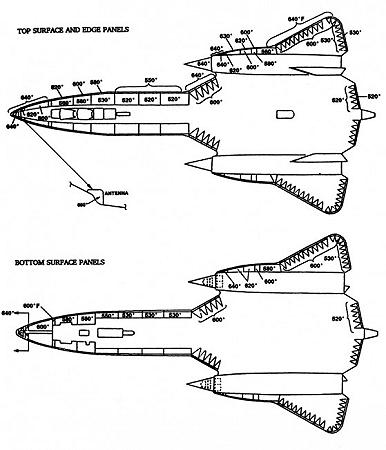
Temperature attese nella pannellatura esterna in gradi Farheneit. (Fonte: USAF).
Se per la realizzazione dell’interno dei motori è possibile utilizzare super materiali come leghe di cobalto e nichel, per poter costruire la struttura portante e la copertura dell’aereo bisogna necessariamente pensare ad altre soluzioni più leggere (per poter arrivare a quote elevate con la propulsione a disposizione) e possibilmente economiche.
Andiamo a vedere quali sono le possibilità che si presentano al team di progettisti:
- Leghe di alluminio – le più diffuse nel settore aeronautico, presentano buone caratteristiche, peso ridottissimo e ottima lavorabilità. Ma tutte hanno temperatura di fusione inferiore ai 700° e in generale pessima resistenza in temperatura. Non utilizzabili.
- Acciai – teoricamente molto resistenti meccanicamente e termicamente, hanno però un peso troppo elevato per poter pensare di essere utilizzate in grandi quantità. Non utilizzabili.
- Compositi strutturali – teoricamente ottimi (e al giorno d’oggi stanno rimpiazzando gli altri materiali in molte applicazioni), ma al tempo della progettazione dei Blackbird troppo acerbi per realizzare strutture portanti.
Queste sono (negli anni ’60 come oggi) le tre categorie principali di materiali strutturali, ma, con grande sconforto di Johnson & Co., nessuna di esse si presta ad essere utilizzata per i nuovi velivoli.
Che fare? Rinunciare al progetto cercando di ridimensionarne i requisiti?
A qualcuno però viene in mente un’altra categoria di materiali, fresca fresca di “scoperta” che sta facendo un gran parlare di sé…
Le leghe del titanio
Ebbene sì, si sta parlando proprio di loro, le ultime new entry nel magico mondo dei materiali, uscite dai laboratori di ricerca nemmeno vent’anni prima.
Ma perchè sono davvero così interessanti?
Il pregio principale di queste leghe risiede nel fatto che riescono ad abbinare proprietà meccaniche paragonabili (ed in alcuni casi superiori) a quelle degli acciai più performanti con un peso specifico che è circa la metà.
Aggiungiamoci che hanno una temperatura di fusione attorno ai 1700° ed un’ottima resistenza a caldo ed abbiamo sulla carta il materiale perfetto.
Oppure no?
Il fatto è che le leghe di titanio presentano sì caratteristiche meravigliose, ma si portano dietro anche una marea di difetti e complicazioni:
- È un metallo giovane – Il titanio è stato estratto per la prima volta in forma metallica nel 1910, in quegli anni lo si sta studiando intensamente solo nelle università ed è stato usato pochissimo in altri ambiti.
- Altissima temperatura di fusione – oltre al fatto che richiede trattamenti aggiuntivi del minerale prima di poter essere fuso, richiede una tecnologia estremamente complessa e costosa (raggiungere i 1700° non è uno scherzo sia energeticamente sia per le attrezzature coinvolte).
- Lavorazione ancora sperimentale – tutte le tecnologie consolidate per la formatura degli altri materiali (asportazione di truciolo, deformazione plastica, trattamenti termici) vanno ripensate, a causa sia della reattività sia dell’ effetto di “ritorno elastico” marcatissimo.
- Richiede manodopera specializzata – per poter essere utilizzato in carpenteria richiede attrezzature apposite per evitare fenomeni di danneggiamento legati alla contaminazione con particolari agenti chimici durante il montaggio e l’esercizio (come per esempio il cadmio contenuto negli attrezzi o i composti a base mercurio/cloro/fluoro contenuti in adesivi, vernici e cancelleria varia).
- Approvvigionamento scarso – il metallo è molto scarso negli USA e, ironia del destino, il maggior produttore di titanio del mondo è… il tanto odiato “covo di rossi”: l’URSS.
E questi sono solo alcuni dei problemi legati all’utilizzo di questo nuovo materiale e sembra proprio che sia impossibile riuscire ad aggirarli…
Si è di nuovo al punto di partenza, senza una reale soluzione.
Magic Johnson
Come stiamo cominciando ad imparare, a Kelly Johnson la parola “impossibile” non è mai andata troppo a genio e al grido di “Fottesega!” si mette al lavoro come è solito fare.
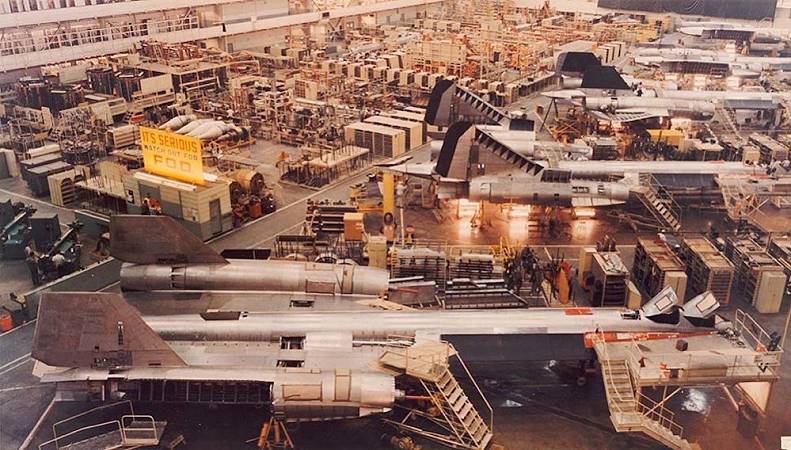
Importa dalla Russia grandi quantità di titanio vergine tramite una serie di società “farlocche” create ad hoc.
Sviluppa tutta una serie di nuove tecnologie di colata, formatura e lavorazione per le nuove leghe.
Si inventa pure nuovi metodi di testing e di controllo qualità per verificare le proprietà dei nuovi manufatti.
Realizza i primi pezzi dei suoi prototipi con queste nuove tecnologie e, raffinando di volta in volta le sue conoscenze a partire dagli errori commessi, riesce ad ottenere componenti affidabili e precisi.
Ci prende talmente gusto che decide di realizzare qualcosa come il 93% in peso del mezzo in titanio.
In particolare per la realizzazione dei Blackbird si sono scelte tre tipologie di leghe di titanio di differente composizione e storia termica:
- A-110AT – 5% alluminio e 2.5% di stagno.
- B-120VCA – 13% vanadio, 11% cromo e 3% alluminio.
- C-120AV – 6% alluminio e 4% vanadio.
In aggiunta a queste tre leghe che vanno a rappresentare la stragrande maggioranza del volume del mezzo, abbiamo l’utilizzo di un acciao inox in alcune piccole parti e di alcune superleghe base nichel (Renè 41 e Hastelloy-X) nella zona dei propulsori, dove si superano localmente i 1200°C.
La costruzione della struttura
Come tutti i velivoli, anche la struttura dei Blackbird è realizzata con uno “scheletro” interno rivestito da pannellature per mantenere aerodinamicità e pesi contenuti.
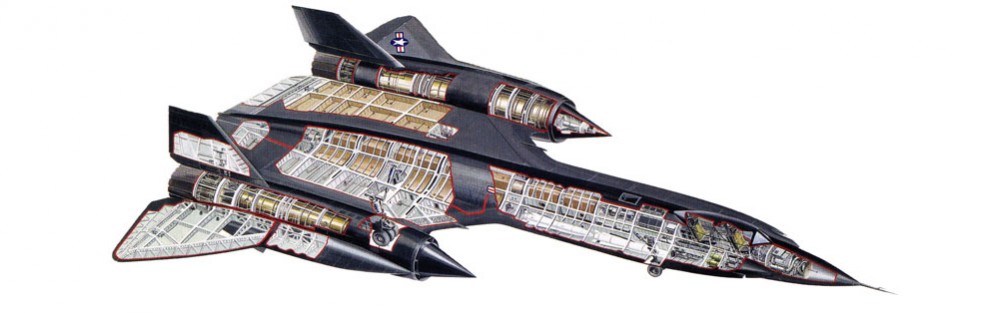
Per comodità di assemblaggio in cantiere vengono costruiti separatamente i vari sotto assiemi (indicati nel grafico seguente) che vengono poi uniti nelle fasi finali.
Andiamo a vederli un po’ più nel dettaglio.
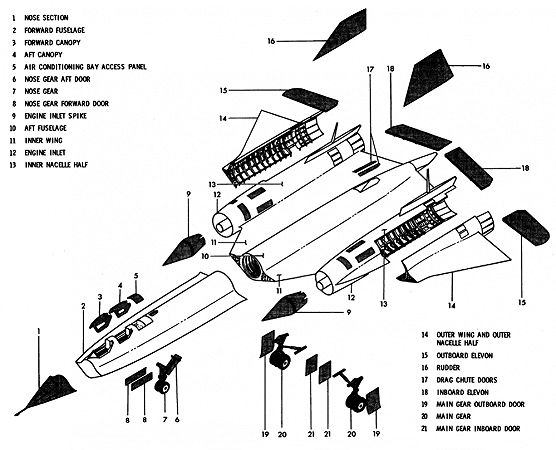
Schema esplicativo delle varie parti della struttura dell’ SR-71 (Fonte: USAF).
Partendo dalla parte anteriore troviamo una delle due metà della fusoliera cilindrica, costituita da una serie di sezioni circolari collegate fra di loro perimetralmente, a formare un lungo tubo, separato in due all’altezza dell’inizio delle ali.
In questa struttura sono ricavati gli alloggiamenti per i piloti e per tutte le attrezzature più delicate di spionaggio e navigazione, nonchè gli agganci per i due caratteristici profili laterali (“chines“) fondamentali per la resa aerodinamica del Blackbird. Trovano posto anche il carrello anteriore ed il muso intercambiabile.
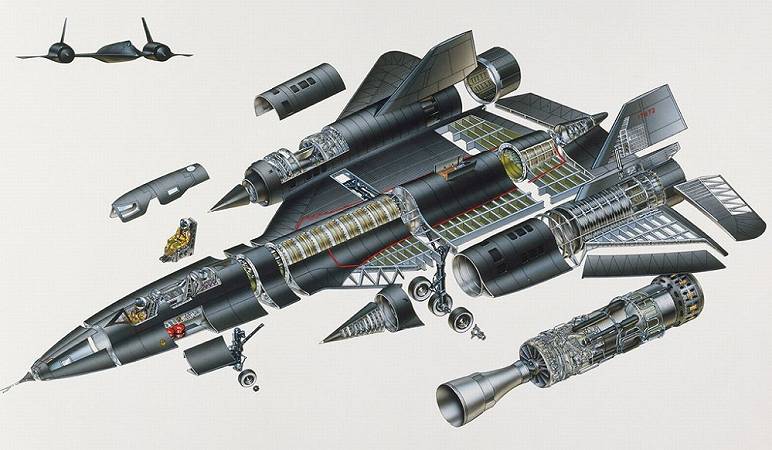
Procedendo verso il retro troviamo la parte più massiva, che ospita la “forza bruta” del mezzo, nella quale un complesso intreccio di longheroni, bulkhead e travature va a creare un solido collegamento tra gli alloggiamenti dei motori (in inglese “nacelles“) e la fusoliera posteriore.
La disposizione dei vari elementi va a creare un insieme di “scatole” collegate fra di loro nelle quali possono essere ospitati tutti i vari componenti interni (come le varie celle dei serbatoi, tubature, cavi e i sistemi delle due ruote estraibili del carrello), fungendo al contempo da superficie alare una volta rivestite.
Muovendosi ora verso l’esterno andiamo a concentrarci sulle nacelles, che presentano un design tutto particolare, dettato dal ruolo che devono ricoprire.
Partendo dal presupposto che queste due sedi cilindriche servono ad ospitare e proteggere i due potenti motori dell’SR-71, possiamo anche immaginare che se fossero realizzate come strutture “monolitiche” le operazioni di estrazione e manutenzione dei propulsori diventerebbero parecchio complicate.

Per ovviare al problema ciascuna sede è divisa verticalmente in due metà, delle quali la più interna è saldata alla struttura, mentre la più esterna è incernierata in alto all’interna, in modo da permettere un moto “basculante”.
Come si può vedere nell’immagine riportata, l’idea ricorda un po’ quella del cofano delle automobili, e risulta estremamente comoda nelle operazioni di manutenzione e di movimentazione a terra.
Per finire la nostra rapida carrellata, sulla metà più esterna delle nacelles sono fissate le due parti terminali delle ali e, sempre sul retro dell’aereo, trovano posto tutti i vari dispositivi ausiliari, come gli alettoni e gli stabilizzatori.
La pannellatura: le rughe
Una volta assemblato lo scheletro portante, bisogna trovare un modo efficace per rivestirlo completamente, donando al mezzo le sue proprietà aerodinamiche e proteggendone l’interno.
Gli ingegneri si sono resi però conto che una semplice ricopertura continua e liscia, anche se realizzata in lega B-120VCA, in un regime di stress termico come quello previsto non sarebbe stata in grado di accomodare le inevitabili dilatazioni, portando alla rottura ed al distacco in pochissimo tempo.
Come primo espediente si è pensato di ricoprire le zone più sollecitate e delicate con dei pannelli dello stesso materiale, ma di nuova concezione caratterizzati da varie scanalature sulla superficie esterna (visibili in foto) alle quali sono fatti corrispondere dei corrugamenti sulla superficie interna.
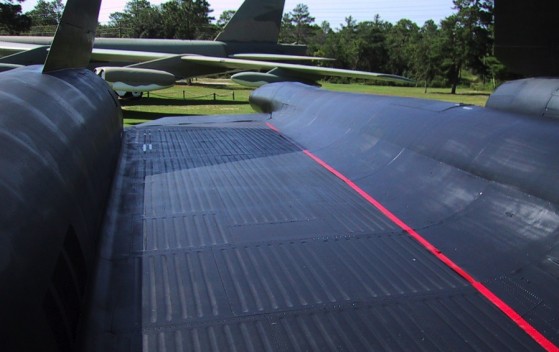
Un tale accorgimento, a prima vista banale, permette ai pannelli di espandersi liberamente, “deviando” il volume di materiale “in eccesso” verso l’interno del velivolo senza andarne ad intaccare la resa aerodinamica ed anzi incrementandone leggermente la rigidezza.
Tuttavia un altro fenomeno è stato osservato dopo i primi voli di test: il fatto che il carburante sia a contatto per gravità con la parte inferiore dei serbatoi (e quindi della fusoliera) la rende più fredda rispetto a quella superiore, rischiando di avere una differenza di deformazione notevole fra le due zone, nonostante l’accorgimento dei pannelli “rugosi”.
Per ovviare a ciò si è andati a modificare la modalità con la quale i pannelli sono fissati alla struttura, saldando e fissando in posizione i pannelli inferiori (anche per limitare le perdite di carburante) ed adottando per quelli superiori degli appositi fermi di nuova concezione che permettono un piccolo slittamento e un’agevole rimozione, facilitando così anche le riparazioni e le ispezioni.
Approccio stealth: i primi compositi
Superate le difficoltà più immediate, rimane da affrontare lo spinoso problema della RCS.
Qualche accorgimento è stato adottato durante le fasi di design, come detto nello scorso articolo, ma i ragazzi degli Skunk Works devono ingegnarsi a cercare un ulteriore contributo per la riduzione dell’impronta radar nell’uso intelligente dei materiali.
Creano quindi un tipo di composito particolare, progettato per avere una, seppur minima, capacità radar assorbente e lo inseriscono nelle zone meno sollecitate termicamente e meccanicamente sotto forma di pannellatura “complessa”, formata dall’alternanza di pannelli triangolari in titanio e in composito.
In sostanza vanno a ricoprire con questi nuovi pannelli tutto il profilo più esterno del mezzo.
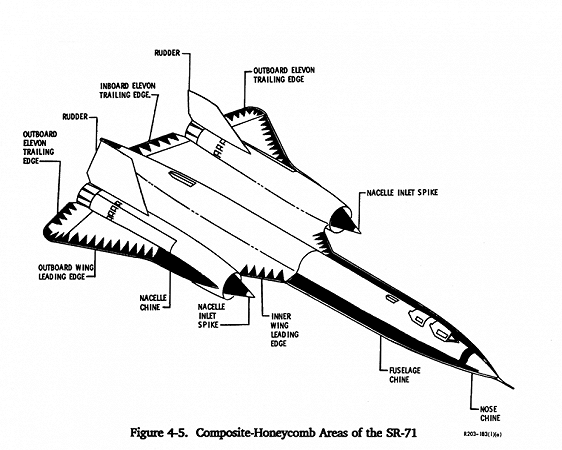
Vi chiederete: “ma come, non avevi scritto che i compositi non esistevano”?
Ni. Nel senso che i compositi strutturali come li intendiamo oggi non erano ancora stati progettati (matrice polimerica con tessuti di fibre vetro/carbonio ecc…), ma esistevano compositi d’avanguardia con carica minerale, incapaci di sopportare carichi importanti, ma comunque resistenti a sufficienza per essere utilizzati come copertura.
Nel caso dell’ SR-71 i compositi in questione sono formati da varie lamine di resine siliconiche addizionate con fibre di amianto e di vetro e, su alcuni modelli, la pannellatura in composito è montata sopra un sustrato metallico a “nido d’ape” (honeycomb) per rinforzo.
Pannello in composito danneggiato sotto il quale è visibile la struttura honeycomb di rinforzo.
Il cockpit
Come è ovvio, non tutta la struttura può essere rivestita da pannellature metalliche o composite, dato che il pilota deve avere visibilità sull’ambiente circostante.
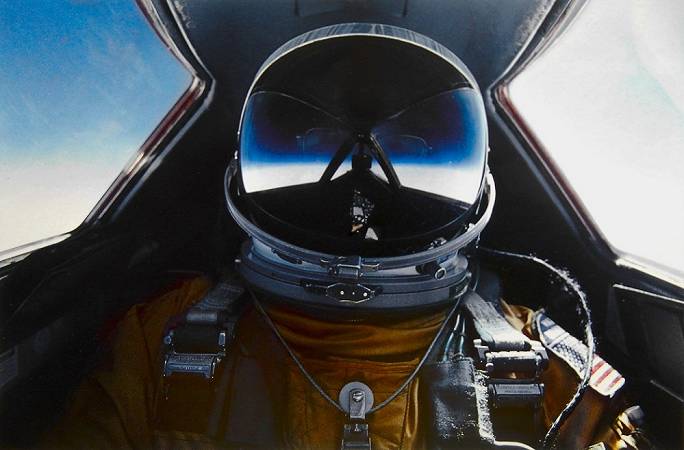
Autoscatto del mitico Brian Shul nella cabina di un SR-71.
Ciò pone di fronte all’ennesima sfida alla temperatura: come realizzare delle finestre sufficientemente resistenti ad urti e dilatazioni?
Ciascun alloggiamento per i piloti è costituito da uno scheletro in titanio, al quale sono agganciati i vari “gruppi finestra”, ognuno dei quali consiste in un due pannelli, spessi circa 1 cm, separati da un’intercapedine d’aria con la funzione di isolante termico.
L’intercapedine non è completamente isolata dall’esterno, in modo da rendere possibile anche un effetto di rimozione di eventuale condensa.
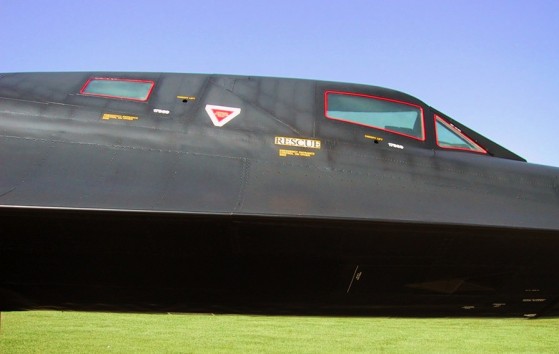
Lo strato più esterno dell’assieme è formato da una singola lastra di vetro temprato, mentre lo strato interno da due lamine di vetro inframezzate da una lamina di resina siliconica, analogamente a quanto accade nei moderni parabrezza.
Pausa di riflessione…
Stavolta prima di passare ai saluti e alle fonti, vorrei trattenervi ancora qualche attimo per farvi vedere alcune immagini che mi hanno particolarmente colpito:
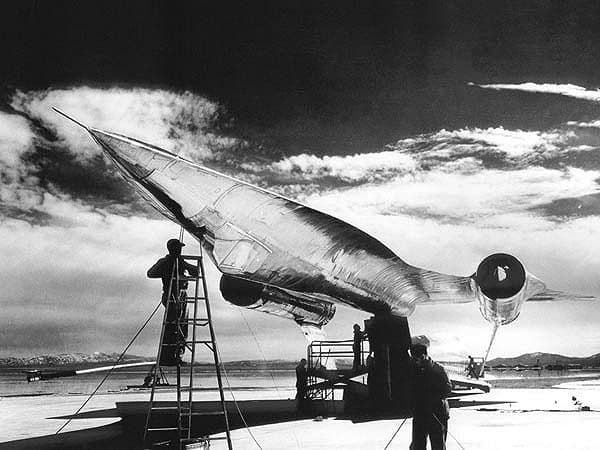
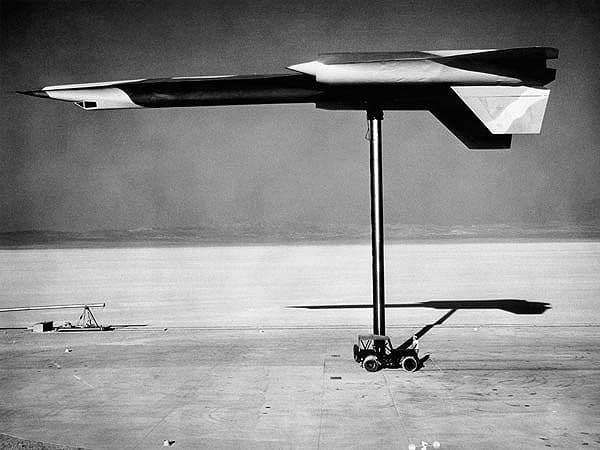
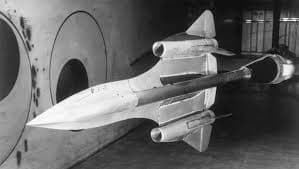
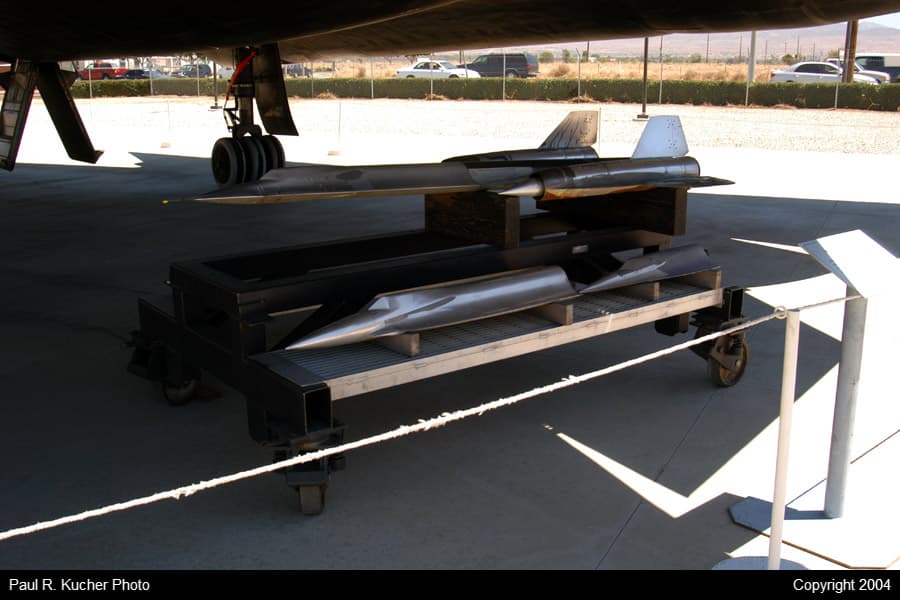
In questi quattro scatti sono essenzialmente riassunti tutti i “potenti” mezzi di simulazione a disposizione all’epoca.
Provate a pensare a cosa abbia voluto dire progettare e costruire la sagoma aerodinamica di un mezzo così estremo avendo a disposizione nient’altro che un modellino in scala per i test nella galleria del vento.
E pensate a quanti inconvenienti si possono avere quando l’unico modo di avere un’idea sulla risposta radar è quello di realizzare un modello mockup a grandezza reale per testarlo “a testa in giù” in mezzo al deserto.
Infine vorrei farvi notare che non si va troppo lontano dalla verità se si afferma che gran parte dei processi produttivi che ci permettono oggi di avere a disposizione oggetti in titanio nella vita di tutti i giorni (protesi, dispositivi medici, componentistica meccanica, turbine ecc….) li dobbiamo in buona parte proprio a quel team di pazzi visionari capitanati da Kelly Johnson che ne hanno gettato le basi.
Conclusioni
Così siamo arrivati di nuovo in fondo ad un nuovo articolo, sperando come sempre di avervi raccontato qualcosa di interessante e solleticato qualche curiosità.
Se avrete voglia di seguirmi ancora in questo strano viaggio che stiamo facendo su LN, nella prossima puntata andremo a conoscere più da vicino il cuore pulsante dei Blackbird, il vero responsabile dell’alone di leggenda che circonda questo mezzo: il motore J58.
Stay tuned!
Questo articolo è parte di una serie: #Blackbird
Fonti Principali:
- Design and Development of the Blackbird – principale fonte tecnica.
- To Keep The Peace They Flew Alone…Unarmed – una vera miniera d’oro di testimonianze/curiosità/dati a cura di uno degli addetti ai lavori.
- SR-71 Online – altra incredibile fonte curata da un appassionato. Gallerie fotografiche di gran parte dei velivoli esistenti.
- Video Documentario “the Silent Vigil” Discovery Channel
- Lockheed: creating the Blackbird
- Lockheed U-2 wiki (eng)
- Lockheed SR-71 wiki (eng)