Alluminio: quando riciclare conviene
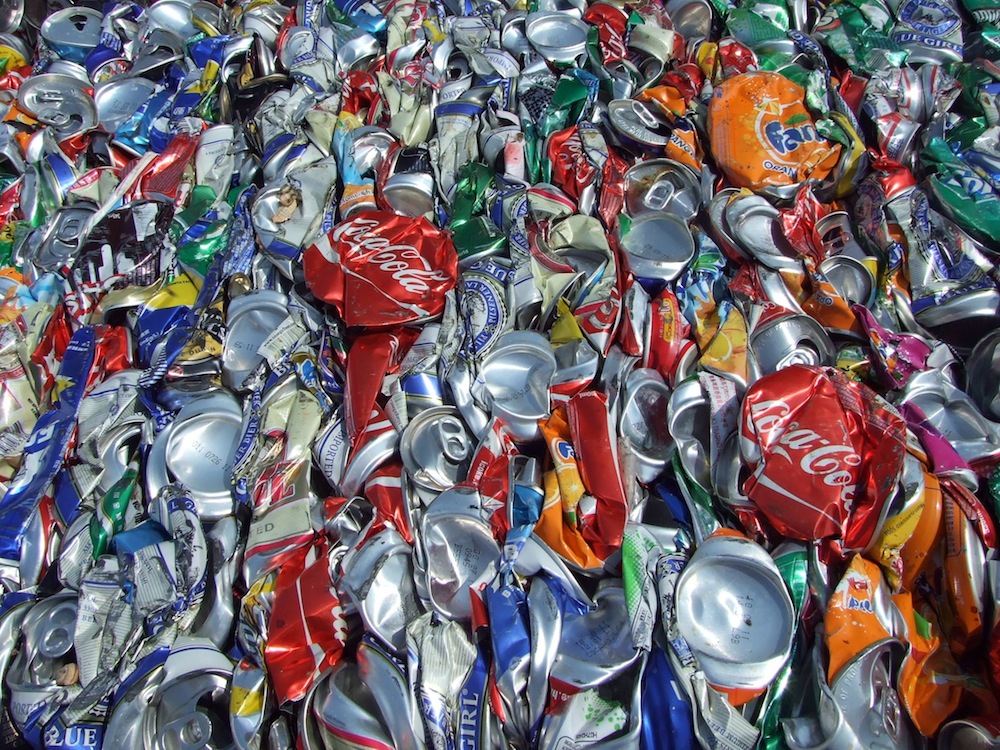
Rieccoci qui per la seconda puntata del nostro piccolo viaggio! Abbiamo parlato e discusso qui dello spinoso problema delle plastiche e del loro destino nel nostro globo preferito, ora è arrivato il momento di dare uno sguardo ad un altro materiale che ci fa compagnia ogni giorno, ma che forse tanto bene poi non conosciamo: l’alluminio.
Ora prendetevi un attimo (se poi sforate il tempo di lettura previsto da LN andate al lamentarvi col capo) e guardatevi intorno. Sia che voi siate in ufficio, alla vostra scrivania, in cucina o in qualunque altro posto, state sicuri che attorno a voi si trova una miriade di oggetti, più o meno grandi, che gran parte di noi chiama “di ferro”, ma che in realtà non sono altro che alluminio.
Sto parlando di pentole, caffettiere, infissi, portachiavi, lampade, cerniere, lattine, penne… Ma alla fin fine che cos’è l’alluminio? Da dove viene? E che me ne faccio quando non mi serve più?
Le necessarie presentazioni
Prima di avventurarci nel mondo della produzione e del riciclo dell’alluminio facciamo un attimo il punto su cosa aspettarci da questo metallo.
Si tratta di un metallo giovane (noto industrialmente da poco più di 100 anni) con proprietà meccaniche discrete (superiori a quelle di molte plastiche e fra le migliori nella grande famiglia delle leghe non ferrose di uso comune) e soprattutto caratterizzato da un’elevata leggerezza. A parità di volume, infatti, un pezzo in alluminio pesa meno della metà di un pezzo in acciaio.
Oltre a questo presenta molte altre caratteristiche interessanti: è un ottimo conduttore, resiste bene in ambienti aggressivi (la sua “ruggine” invece di danneggiare la superficie forma un film compatto che la protegge), non è tossico, si deforma poco con le variazioni di temperatura, è molto lavorabile…. Insomma sembra essere il migliore amico di ogni progettista.
Bisogna notare che l’alluminio puro ha pochi utilizzi pratici (principalmente chimica ed elettrotecnica) e industrialmente si utilizza abbinato ad altri elementi chimici, come il rame o il magnesio solo per citarne alcuni, andando così a formare le varie famiglie di leghe previste da normativa, ciascuna con i suoi pregi e difetti.
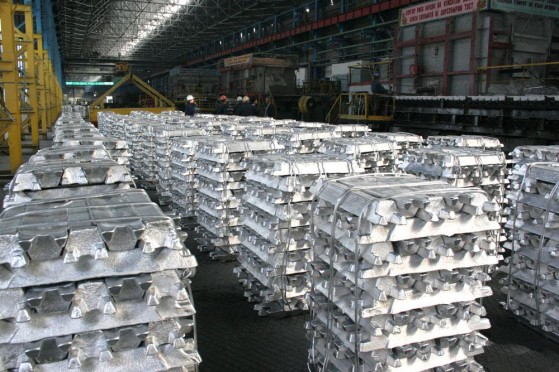
I processi produttivi per ottenere un oggetto in alluminio sono tanti e ci vorrebbero almeno una decina di articoli a illustrarne anche solo alcuni, ma necessitano tutti di una procedura iniziale comune. Infatti bisogna portare a fusione dei “blocchi” di alluminio puro, fare le necessarie aggiunte chimiche (a volte “sparando” letteralmente delle lattine con dentro il composto desiderato nel metallo fuso) e colare il tutto in varie forme.
Ora a questo proposito bisogna fare una distinzione molto importante, in base alla provenienza di questi “blocchi” di alluminio, fra:
- Alluminio primario – derivato dal minerale, massima purezza
- Alluminio secondario – derivato dal riciclo, meno costoso
Primario: come si ottiene?
Come avrete sicuramente capito, non è tutto oro ciò che luccica (il primo che fa la battuta vince una mentina ciucciata autografata dal sottoscritto).
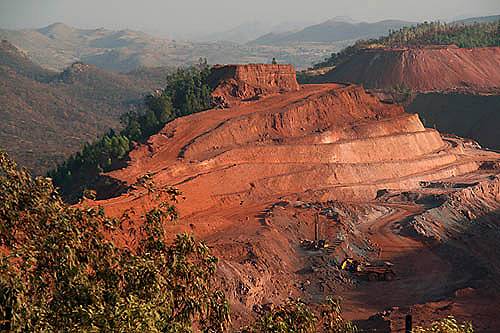
Difatti in natura l’alluminio è presente in grosse quantità ma, sfortunatamente per noi, non lo si trova puro, nè tantomeno combinato con i suoi elementi di lega, ma piuttosto nella forma di ossido [latex] Al_2 O_3 [/latex], altimenti detto allumina, presente in vari minerali, il più famoso e usato dei quali è la bauxite, ricco di ferro (da qui il colore rossastro) ed estratto in miniere a cielo aperto.
Qualcuno di voi si starà forse domandando: e dov’è il problema?
Il problema è semplice: l’alluminio puro fonde a poco meno di 700°, l’allumina a circa 2000° e viene difatti usata per realizzare una buona parte dei materiali refrattari usati per i forni più performanti nell’industria dell’acciaio.
Ciò implica che non posso ragionevolmente pensare di scaldare fino a separare l’ossido, ma devo inventarmi qualcos’altro.
La via elettrolitica
Verso la fine del 1800 ci si è molto arrovellati a riguardo e si è sviluppata una procedura, che è usata ancora oggi, composta in due step successivi:
- il processo Bayer – permette la separazione della sola allumina da tutte le altre impurezze presenti nel minerale proveniente dalle cave
- il processo Hall-Heroult (smelting)– permette l’ottenimento dell’alluminio metallico a partire dall’allumina
Per chi fosse interessato ai dettagli tecnici metto sotto approfondimento una mia versione semplificata del processo, rimandando a wiki o a siti specializzati per approfondimenti vari.
[more]
Per tutti i “chemical nazi”, premetto che ciò che segue in alcune reazioni può non essere sempre stechiometricamente ortodosso, dato che è pensato più per essere un’introduzione che un’analisi accurata.
Processo Bayer
Il processo Bayer essenzialmente utilizza soda caustica per isolare l’ossido di alluminio dalle altre sostanze e separarlo meccanicamente.
Il minerale di partenza, la bauxite, presenta circa il 50% in peso di allumina, e altri ossidi, principalmente a base ferro. Dopo aver macinato e dato una prima pulita macroscopica alla polvere così ottenuta, la si mischia con soda caustica e acqua in appositi reattori, a temperature comprese fra i 100° e i 200° e a pressione fra le 5 e le 10 atm.
L’unica reazione promossa è quella che vede la soda caustica legarsi con l’allumina presente nel minerale, “estraendola” e creando un composto complesso:
[latex]Al_2O_3+ 2NaOH + 3H_2O \rightleftharpoons 2NaAl(OH)_4 [/latex]
Ho quindi la formazione di un “pastone” semiliquido in cui ho disciolto l’alluminato e tutte le altre impurezze sono presenti allo stato solido.
Risulta possibile rimuovere i composti indesiderati tramite filtrazione (dando origine ai famosi “fanghi rossi” altamente inquinanti) e ottenere una soluzione pura di solo alluminato sodico.
A questo punto posso far cristallizzare l’allumina in forma idrata praticamente effettuando il passaggio inverso a quello di prima, riottenendo la soda caustica che è reimmessa nel processo:
[latex]NaAl(OH)_4 \rightleftharpoons Al(OH)_3 + NaOH [/latex]
Infine non mi resta che calcinare l’ossido idrato, scaldandolo ed eliminandone l’acqua per ottenere finalmente allumina altamente pura.
Processo Hall-Heroult: lo smelting
Dopo aver fatto tutta sta fatica a ripulire l’allumina ci ritroviamo con lo stesso problema di partenza: isolare il metallo.
Questi due figaccini di Hall ed Herolut hanno sviluppato pressapoco nello stesso momento e indipendentemente l’uno dall’altro un metodo ingegnoso, impiegando l’elettrolisi.
Si sono accorti che impiegando l’acqua come elettrolita non si andava da nessuna parte, dato che gran parte dell’energia andava per scindere le molecole di acqua, quindi si è pensato di impiegare un composto water free particolare, detto criolite, che ha la caratteristica di avere una temperatura di fusione prossima ai 1000° e di permettere allo stato liquido una dissociazione dell’allumina (in piccole quantità).
Quindi un generico impianto di smelting è composto da molte celle in parallelo, ciascuna delle quali è composta da una vasca in acciaio, con all’interno un catodo e un anodo in grafite, riempita di criolite.
In ogni singola cella si fa passare (taaaaaaanta) corrente fra anodo e catodo portando a fusione la criolite, e si aggiungono piccole quantità di allumina nel bagno.
In queste condizioni si ha che in prossimità dell’anodo in grafite l’allumina [latex] Al_2O_3 [/latex] si separa, l’alluminio metallico va a depositarsi sul fondo in prossimità del catodo, mentre l’ossigeno va verso l’anodo dove si lega con il carbonio che costituisce l’anodo stesso creando [latex] CO_2 [/latex].
Quando si è accumulato alluminio a sufficienza sul fondo, con sistemi a sifoni lo si raccoglie e lo si porta fuori dalla cella, rabboccando al contempo nuova allumina a rimpiazzare quella che è andata dissociandosi durante il processo.
[/more]
I costi del primario
Al di là dei dettagli dei vari processi, è importante notare che essi hanno un costo elevatissimo, sia dal punto di vista logistico sia soprattutto dal punto di vista energetico.
Difatti per ottenere una tonnellata di alluminio sono necessari:
- circa quattro tonnellate di minerale (bauxite)
- circa 400 kg di elettrodo in grafite (anodo)
- circa 14000 kWh di energia elettrica solo per la parte elettrolitica del processo
Tutto ciò ha un costo molto elevato, tenendo conto che bisogna poi aggiungere tutti i costi relativi all’abbattimento dei fumi (veramente tanta CO2) e dei fanghi inquinanti del processo Bayer, i costi di gestione degli impianti e mille altri fattori, a fronte di un prezzo del metallo vincolato dal mercato.
Giusto per dare due cifre, il prezzo dell’alluminio primario si attesta attorno ai 1400$/ton, mentre, nella migliore delle ipotesi possibili per l’azienda produttrice, solo i costi dell’energia elettrica del processo di smelting ammontano a ben un terzo di questa cifra.
It has been repeatedly stated that some 60-70% of aluminum smelters are losing money. Electricity alone is generally accepted as representing about a third of the cost of aluminum ingot. […] Even for those smelters still smart enough or lucky enough to be tied at power costs of one-third of the ingot price at $1300/ton they will be doing well to break even. Add in the fact many smelters are running at well below optimum capacity and the unit price per ton produced suggests they are indeed losing money.
Copyright © 2013 MetalMiner link all’articolo originale
In fin dei conti è un fatto reale che la produzione di alluminio primario al giorno d’oggi stia diventando sempre più una scommessa che una vera fonte di guadagno, come dimostrano i recenti avvenimenti che coinvolgono l’Alcoa, azienda da sempre leader del settore, che ha deciso di chiudere l’impianto sardo a causa dei costi troppo elevati.
L’alluminio secondario
Tutto questo (lungo) discorso ci è servito per farci un’idea spero un po’ più chiara del grande onere che è per l’industria estrarre l’alluminio “vergine” dal minerale e della grandissima importanza che, proprio grazie a questo, assume il riciclo.
Difatti, anche se il metallo è molto giovane, e molti dei prodotti dell’industria pesante devono ancora arrivare per la prima volta a fine vita, ci sono un sacco di oggetti di uso comune che hanno una durata molto breve e che possono andare ad alimentare “la macchina del riciclo”, con l’obiettivo di fornire nuova materia prima virtualmente a costo zero, saltando l’intera costosissima fase di estrazione.
Bisogna però distinguere fra due tipi di “riciclatori”, ovvero:
- Remelters – coloro che trattano solo scarti interni, cioè pezzi difettosi oppure scarti di lavorazione come trucioli, sfridi, bave ecc… Forniscono alluminio di elevata purezza.
- Refiners – quelli meno “schizzinosi”, si occupano di gestire i rifiuti comuni, producendo alluminio leggermente meno puro.
Riciclo in breve
Illustriamo brevemente gli step che costituiscono il processo di riciclo degli scarti in alluminio:
- Raccolta, frantumazione e separazione – i rifiuti vengono puliti, macinati e l’alluminio viene separato dagli altri materiali eventualmente presenti
- Delaccaggio – si procede ad una combustione controllata per eliminare le tracce di vernice
- Compattazione – si compattano i frammenti in dischetti o cilindretti per avere una densità maggiore (possono affondare quando li fondo e sciogliersi meglio)
- Fusione, controllo di composizione e colata
Un esempio principe di manufatti riciclabili è offerto dalle lattine alimentari, che presentano facilità di raccolta assieme ad una vita utile molto breve ed una grande diffusione nel mercato.
Giusto per fare qualche cifra generica si stima che circa il 30% del totale dell’alluminio prodotto ed utilizzato industrialmente provenga da riciclo, nel caso particolare delle lattine questa percentuale sale fino all’80%.
Conclusioni
Ho cercato nel mio piccolo di mostrarvi quanto complessa sia la produzione di uno dei materiali a cui ci stiamo sempre più abituando e che sempre più spesso diamo per “scontato” ed economico.
La realtà è che purtroppo ottenere alluminio è un processo estremamente costoso ed estremamente inquinante ma ciò comporta anche che i rifiuti, almeno in questo caso, assumono proprio per questo motivo un valore elevatissimo.
Per una volta quindi anche i produttori di manufatti in alluminio hanno un grosso interesse “naturale” nel valorizzare e sfruttare i rifiuti e, se noi cittadini ci impegneremo nel nostro piccolo a differenziarli e raccoglierli, possiamo stare sicuri che l’industria farà la sua parte, ridando una nuova vita ai nostri scarti!
Riciclate gente, riciclate!
Come sempre buona parte di ciò che ho illustrato deriva da conoscenze raccolte durante i corsi, ma sul web si trovano molte fonti di informazioni, alcune delle quali davvero ben fatte, riguardo ai processi di produzione. Ne linko solo alcune:
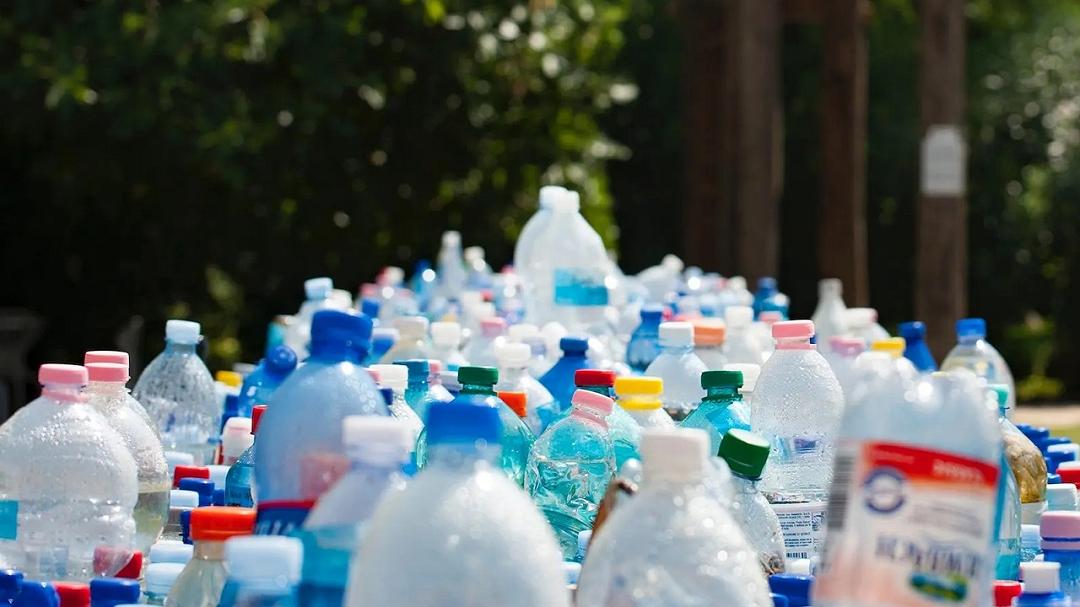
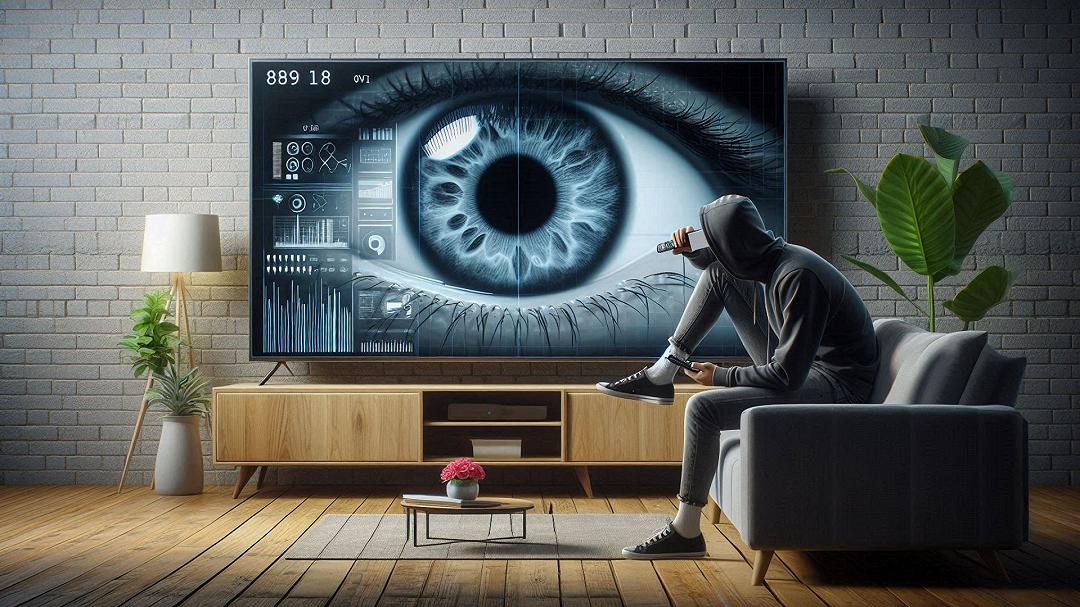
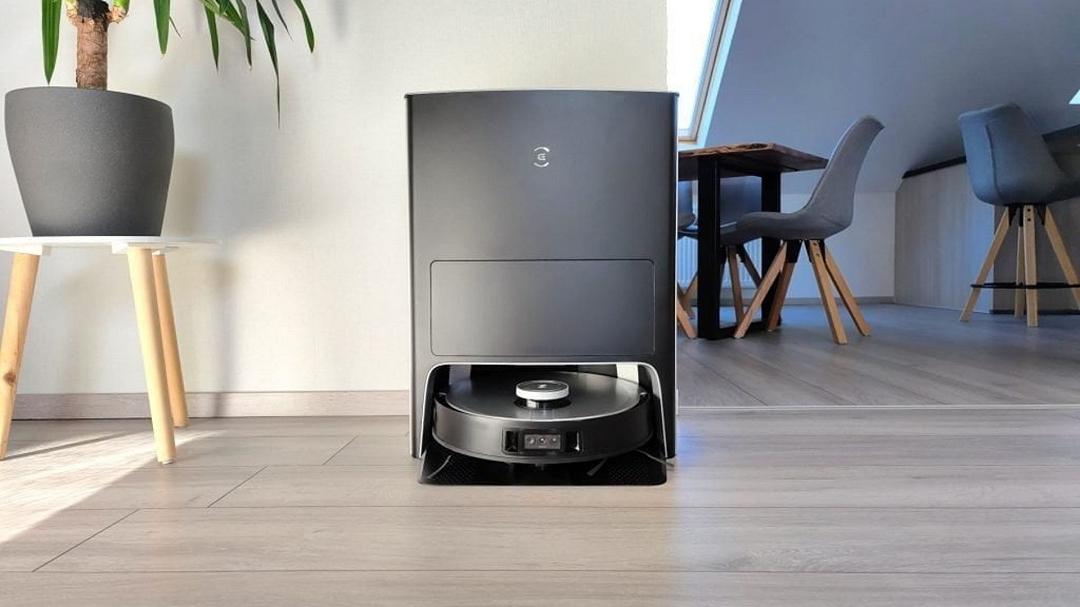