L’alluminio riciclato consente di risparmiare energia, emissioni e autonomia delle batterie
Il nuovo processo di produzione produce parti di veicoli in alluminio ad alta resistenza che riducono i costi e sono più rispettosi dell'ambiente
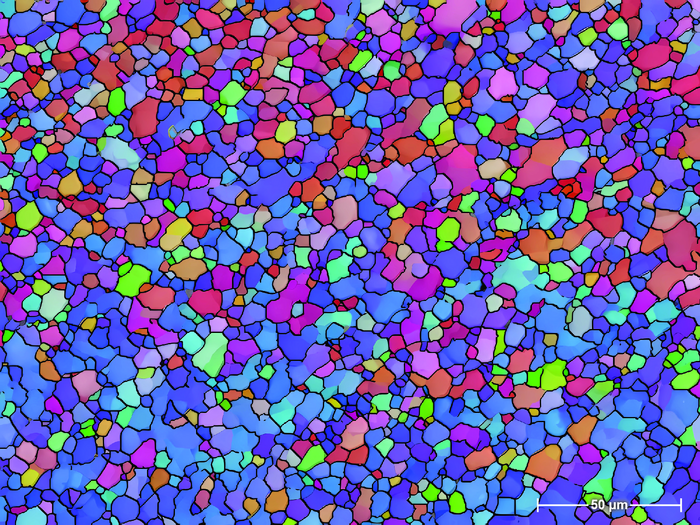
La microstruttura di un trapezio di alluminio mostra una granulometria altamente raffinata e uniforme, fondamentale per ottenere un prodotto robusto e affidabile
I rottami di alluminio possono ora essere raccolti e trasformati direttamente in nuove parti di veicoli grazie a un processo innovativo sviluppato dall’industria automobilistica, in particolare per i veicoli elettrici. Oggi il Pacific Northwest National Laboratory del Dipartimento dell’Energia, in collaborazione con Magna, azienda leader nelle tecnologie per la mobilità, presenta un nuovo processo produttivo che riduce di oltre il 50% l’energia incorporata e di oltre il 90% le emissioni di anidride carbonica, eliminando la necessità di estrarre e raffinare la stessa quantità di minerale di alluminio grezzo. L’alluminio leggero può anche contribuire ad aumentare l’autonomia dei veicoli elettrici. Il processo brevettato e premiato Shear Assisted Processing and Extrusion (ShAPE™) raccoglie gli scarti e gli avanzi di alluminio della produzione automobilistica e li trasforma direttamente in materiale adatto alle parti di nuovi veicoli. Ora è in fase di scalata per produrre parti in alluminio leggero per i veicoli elettrici. Il progresso più recente, descritto in dettaglio in un nuovo rapporto e in un articolo di ricerca di Manufacturing Letters, elimina la necessità di aggiungere alluminio di nuova estrazione al materiale prima di utilizzarlo per nuovi pezzi. Riducendo il costo del riciclo dell’alluminio, i produttori potrebbero essere in grado di ridurre il costo complessivo dei componenti in alluminio, consentendo loro di sostituire l’acciaio.
“Abbiamo dimostrato che le parti in alluminio formate con il processo ShAPE soddisfano gli standard dell’industria automobilistica per quanto riguarda la resistenza e l’assorbimento di energia“, ha dichiarato Scott Whalen, scienziato dei materiali del PNNL e ricercatore principale. “La chiave è che il processo ShAPE rompe le impurità metalliche nel rottame senza richiedere una fase di trattamento termico ad alta intensità energetica. Già questo fa risparmiare molto tempo e introduce nuove efficienze“. Il nuovo rapporto e le pubblicazioni di ricerca segnano il culmine di una collaborazione quadriennale con Magna, il più grande produttore di componenti auto del Nord America. Magna ha ricevuto un finanziamento per la ricerca collaborativa dal programma del DOE Vehicle Technologies Office, Lightweight Materials Consortium (LightMAT). “La sostenibilità è al centro di tutto ciò che facciamo in Magna”, ha dichiarato Massimo DiCiano, Manager Materials Science di Magna. “Il processo ShAPE è un’ottima prova di come stiamo cercando di evolvere e creare nuove soluzioni sostenibili per i nostri clienti”.
Estrusioni realizzate da ShAPE da rottami industriali AA6063 che producono (a) profili circolari, (b) quadrati, (c) trapezoidali e (d) trapezoidali a due celle.
CREDIT :(Immagine per gentile concessione di Scott Whalen | Pacific Northwest National Laboratory)
I vantaggi dell’alluminio
Oltre all’acciaio, l’alluminio è il materiale più utilizzato nell’industria automobilistica. Le proprietà vantaggiose dell’alluminio lo rendono un componente automobilistico interessante. Più leggero e resistente, l’alluminio è un materiale chiave nella strategia di realizzare veicoli leggeri per migliorare l’efficienza, sia che si tratti di estendere l’autonomia di un veicolo elettrico o di ridurre le dimensioni della batteria. Sebbene l’industria automobilistica ricicli attualmente la maggior parte dell’alluminio, prima di riutilizzarlo aggiunge abitualmente alluminio primario di nuova estrazione, per diluire le impurità. I produttori di metalli si affidano anche a un processo secolare di preriscaldamento dei mattoni, o “billette”, come vengono chiamate nel settore, a temperature superiori a 1.000°F (550°C) per molte ore. La fase di preriscaldamento scioglie gli ammassi di impurità come il silicio, il magnesio o il ferro nel metallo grezzo e li distribuisce uniformemente nella billetta attraverso un processo noto come omogeneizzazione.
Il processo ShAPE, invece, realizza la stessa fase di omogeneizzazione in meno di un secondo e trasforma l’alluminio solido in un prodotto finito in pochi minuti, senza bisogno di alcuna fase di preriscaldamento. Per questi esperimenti, il team di ricerca ha lavorato con una lega di alluminio nota come 6063, o alluminio architettonico. Questa lega è utilizzata per diversi componenti automobilistici, come le culle dei motori, i paraurti, le guide del telaio e le finiture esterne. Il team di ricerca del PNNL ha esaminato le forme estruse utilizzando la microscopia elettronica a scansione e la diffrazione a retrodiffusione di elettroni, che crea un’immagine del posizionamento e della microstruttura di ogni particella metallica all’interno del prodotto finito. I risultati hanno mostrato che i prodotti ShAPE sono uniformemente resistenti e privi di difetti di fabbricazione che potrebbero causare la rottura delle parti. In particolare, i prodotti non presentano segni di grandi ammassi di impurità metalliche che possono causare il deterioramento del materiale e che hanno ostacolato gli sforzi per utilizzare l’alluminio riciclato secondario per realizzare nuovi prodotti. Il team di ricerca sta ora esaminando leghe di alluminio a resistenza ancora maggiore, tipicamente utilizzate nelle custodie delle batterie dei veicoli elettrici. “Questa innovazione è solo il primo passo verso la creazione di un’economia circolare per l’alluminio riciclato nella produzione”, ha dichiarato Whalen. “Stiamo ora lavorando per includere i flussi di rifiuti post-consumo, che potrebbero creare un mercato completamente nuovo per i rottami di alluminio secondario”. Inoltre, la tecnologia brevettata ShAPE può essere concessa in licenza per altre applicazioni.